Why Welded Pipes Are the Backbone of the Oil and Gas Industry
Everyday operations in oil and gas rely on components that can handle tough conditions without fail. Among these, welded pipes take center stage, providing the strength and reliability needed for everything from transporting resources over vast distances to performing under high pressures in refineries. Their versatility, durability, and cost-effectiveness make them the backbone of pipelines and processing systems worldwide. Let’s take a closer look at what makes welded pipes such an integral part of the industry.
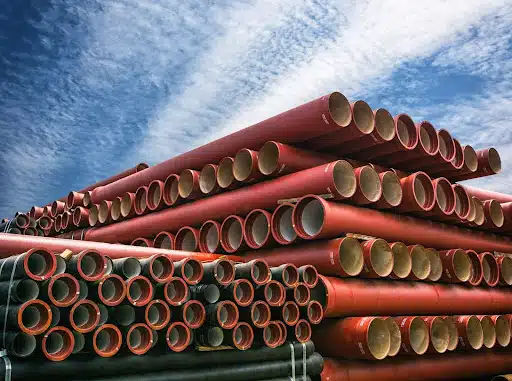
What Are Welded Pipes?
Welded pipes are made by shaping flat steel plates or strips into a tube and welding the edges together to form a strong, reliable seam. Unlike seamless pipes, which are made without any joints, welded pipes come in a wide range of sizes, materials, and specifications, making them a versatile choice for industries like oil and gas. They’re valued not only for their durability but also for being more affordable than other options. This combination of reliability and cost-effectiveness is why welded pipes have become a trusted solution for tough, high-pressure applications.
Key Advantages of Welded Pipes in the Oil and Gas Industry
Key Advantages of Welded Pipes in the Oil and Gas Industry
When it comes to materials for oil and gas operations, welded pipes offer several practical benefits that make them a reliable choice. Here’s why they’re widely used:
- Affordable and Efficient to Produce: The process of welding flat steel plates into pipes is far more economical than creating seamless pipes. This makes welded pipes cost-effective, especially for large-scale projects where budgets matter.
- Available in a Variety of Sizes: One of the biggest strengths of welded pipes is their flexibility. They’re available in several sizes and thicknesses, so it is easy to find the right fit for pipelines handling high-pressure or extreme temperatures.
- Built for Strength and Durability: Thanks to advancements in welding techniques, these pipes are incredibly strong and designed to last—even in demanding environments. They’re made to keep up with the tough conditions of oil and gas operations.
- Resistant to Corrosion and Wear: Welded pipes are built to handle corrosive environments and regular wear and tear. When sourced from a reliable welded pipe supplier, they’ll stand the test of time in pipelines and refineries.
Applications of Welded Pipes in the Oil and Gas Industry
Welded pipes play a vital role in the oil and gas industry, supporting various operations. Here’s how they’re commonly used:
- Transportation of Resources: Whether it’s crude oil, refined products, or natural gas, welded pipes are the backbone of the pipelines that stretch across countries and continents. Their durability ensures resources flow smoothly and reliably to meet global demand.
- Drilling Operations: In drilling, welded pipes are used as casing and tubing to stabilize boreholes and safely extract oil and gas from underground reserves. They’re built to handle the pressure and challenges of these operations.
- Refinery Applications: Refineries rely on welded pipes to move fluids under high pressure and intense heat. Their ability to withstand these tough conditions makes them integral to refining systems.
The Role of Welded Pipes in Ensuring Safety and Efficiency
Safety and efficiency are non-negotiable in the oil and gas industry, and welded pipes play a vital role in achieving both. The welding process creates a strong, tight seam that minimizes the risk of leaks—a critical factor when dealing with hazardous substances like crude oil and natural gas.
To ensure reliability, many suppliers provide pipes that undergo strict quality testing. These include hydrostatic testing, X-ray inspections, and ultrasonic evaluations to confirm the pipes can handle the pressures and demands of their intended applications. Partnering with a dependable welded pipe supplier helps oil and gas companies mitigate risks and maintain safe operations.
On the efficiency front, welded pipes stand out. They’re often lighter than other piping options, making them easier to transport and install, reducing project timelines and labor costs. Additionally, their smooth interior surfaces minimize friction, ensuring better fluid flow and improved overall system performance. This combination of safety, reliability, and efficiency is why welded pipes are a cornerstone of oil and gas infrastructure.
Environmental Considerations
With growing concerns about sustainability, the oil and gas industry is under pressure to reduce its environmental impact, and welded pipes play a valuable role in these efforts. Their manufacturing process is less resource-intensive than other piping options, resulting in a smaller carbon footprint. This makes them a more environmentally conscious choice for large-scale projects.
Durability and corrosion resistance are other key advantages of welded pipes. Their long lifespan means fewer replacements are needed, which helps reduce material waste over time. A trusted welded pipe supplier also offers recyclable products, ensuring the pipes can be reused at the end of their lifecycle—a significant step toward aligning with sustainability goals.
Additionally, welded pipes help prevent leaks in advanced pipeline systems, which minimizes resource loss and reduces greenhouse gas emissions. Their reliability and efficiency in transporting resources safely make them a critical part of the industry’s move toward more sustainable practices. By choosing the right supplier, companies can prioritize performance while supporting environmental responsibility.
When you look closer at the oil and gas industry, it becomes clear that welded pipes are essential to holding it all together. From their cost-effectiveness and adaptability to their role in enhancing safety, efficiency, and sustainability, these pipes have proven their worth time and time again. Partnering with a dependable supplier ensures access to high-quality pipes that meet the demanding standards of this industry.
As the oil and gas sector changes, the importance of welded pipes will only grow. They’re not just pipes—they’re the foundation of a system that powers the world, ensuring energy flows safely and efficiently from source to destination.
FAQ’s
We often recommend welded pipes for the oil and gas industry because they offer a great mix of affordability, durability, and flexibility. They’re tough enough to handle high pressure and temperature while being available in a range of sizes and materials. As a trusted welded pipe supplier, we ensure our customers get exactly what their operations demand.
When comparing welded pipes to seamless ones, it comes down to application and budget. Seamless pipes are ideal for extreme conditions, but welded pipes are a solid, cost-effective alternative that performs exceptionally well in most oil and gas projects. With the right welded pipe supplier, you get both quality and value.
For oil and gas work, we typically supply three main types of welded pipes: electric resistance welded (ERW), longitudinal submerged arc welded (LSAW), and spiral welded pipes. Each has its strengths, depending on the job. We’re always happy to help you decide what best fits your project.
Absolutely. When manufactured with the right processes and materials, welded pipes are built to handle high-pressure environments. We test every pipe to ensure it meets the standards for demanding oil and gas applications, so you can trust they’ll perform when it matters most.
When buying welded pipes, certifications like API 5L, ASTM, and ISO are key—they guarantee quality and safety. We provide full documentation for all our products, so you can feel confident that you’re sourcing from a reliable welded pipe supplier who prioritizes industry compliance and your peace of mind.