Role of Flanges in High-Pressure and High-Temperature Applications in Oil and Gas
In high-pressure and high-temperature systems, like those commonly found in the oil and gas industry, every component plays a key role in keeping things running smoothly and safely. Flanges might not get much attention, but they’re essential for creating secure, leak-proof connections in pipes, valves, and other equipment. Beyond that, they make maintenance and inspections easier, ensuring systems stay reliable over time. In this blog, we’ll take a closer look at flanges for the oil and gas industry—what they do, the materials and standards they rely on, the challenges they face in tough conditions, and the innovations shaping how they’re used today. Whether you work with flanges regularly or are just curious to learn more, this guide has you covered.
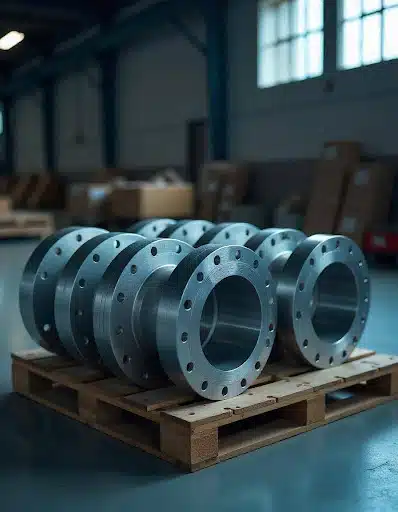
What Are Flanges?
Flanges are vital components in piping systems, connecting pipes, valves, pumps, and other equipment to ensure everything operates safely and efficiently. They’re designed to create a tight seal that prevents leaks, even under high pressure, and are available in various types, such as weld neck, slip-on, socket weld, and blind. Beyond their basic function, flanges make maintenance and inspections easier, essential in industries where reliability and safety are top priorities.
When sourcing flanges, flanges suppliers play a critical role in providing durable, high-performance products that can handle challenging conditions. This is particularly important in the oil and gas industry, where flanges are exposed to extreme pressures, intense heat, and corrosive environments. Working with a trusted supplier ensures the flanges meet strict industry standards, minimizing the risk of leaks or failures. In high-pressure systems, having reliable flanges from the right supplier helps keep operations running smoothly and avoids costly disruptions.
Key Roles of Flanges in High-Pressure and High-Temperature Applications
Flanges do more than just hold things together—they’re critical for keeping systems running safely and smoothly, even in some of the harshest environments imaginable. Here’s how flanges for the oil and gas industry make all the difference:
- Designed for Extreme Conditions: Oil and gas operations often push materials to their limits with high temperatures, intense pressures, and exposure to corrosive substances. Flanges are built to handle these extremes while maintaining their strength and reliability.
- Creating a Reliable Seal: Flanges act as a secure connection point, distributing stress across the joint to prevent leaks or bursts. This is crucial in high-pressure applications where safety and system performance can’t be compromised.
- Making Maintenance Easier: Flanges simplify maintenance by allowing sections of piping to be easily disassembled for inspection or repairs. This reduces downtime and ensures the entire system stays in good working order, even with regular servicing.
- Handling Pressure and Temperature Changes: In refinery pipelines and other high-pressure systems, conditions can change quickly. Flanges are engineered to keep connections secure, even when temperatures fluctuate or pressure spikes suddenly.
- Built to Last: Flanges for the oil and gas industry are made from durable materials that resist wear and corrosion. Their longevity keeps systems running smoothly and reduces the need for frequent replacements, saving both time and money.
Flanges aren’t just another component—they’re a cornerstone of safety, efficiency, and reliability in an industry where there’s no room for error. Their ability to perform under pressure makes them essential in keeping operations moving forward.
Materials and Standards for High-Performance Flanges
Choosing the right material for flanges isn’t just a technical decision—it’s about ensuring they perform safely and reliably, even in tough conditions. Flanges suppliers provide a range of materials designed for different applications. Here’s what to keep in mind:
- Material Options: Flanges are typically made from materials like carbon steel, stainless steel, alloy steel, or nickel-based alloys. The choice depends on what the system demands, such as withstanding high pressure, extreme temperatures, or corrosive environments.
- Best Picks for Oil and Gas: In the oil and gas industry, stainless steel and high-nickel alloys are often preferred because they’re tough against corrosion and built to perform in extreme conditions. These materials hold up well in environments where reliability is critical.
- Standards Matter: Standards like ASME, ASTM, and ISO set the bar for quality and safety. Reliable flanges suppliers make sure their products meet these benchmarks, so you can trust they’ll do the job when it counts.
Challenges and Solutions in High-Pressure and High-Temperature Applications
Preventing leaks and ensuring durability are two of the biggest challenges when using flanges for the oil and gas industry. Here’s how these issues can be tackled effectively:
- Preventing Leaks in High-Stress Systems: In high-pressure and high-temperature setups, even a small issue with a flange can lead to serious problems like equipment damage, downtime, or safety risks. Ensuring a secure seal is critical to keeping things running smoothly.
- Dealing with Material Degradation: Over time, exposure to corrosive chemicals or saltwater can wear down flanges, making them vulnerable to failure. Thankfully, advances in material science now offer flanges that are more resistant to corrosion and fatigue, extending their lifespan.
- Using Protective Coatings and Advanced Gaskets: Specialized coatings can protect flanges in harsh conditions, while high-performance gaskets improve sealing and reduce the chance of leaks. These small upgrades make a big difference in tough environments.
- Focusing on Installation and Maintenance: Proper installation—like tightening bolts to the correct torque—is key to avoiding problems. Regular inspections and maintenance also help catch potential issues early, preventing costly failures down the road.
Innovations in Flange Technology
Flange technology has come a long way to meet the ever-increasing demands of industries like oil and gas. Today’s flanges are built to perform better under tough conditions, with features like advanced surface treatments that improve durability and enhanced sealing mechanisms that help prevent leaks. In some cases, composite materials are being explored for lighter-duty applications, offering a mix of strength and reduced weight. Digital tools, such as simulation software and digital twin technology, are also helping engineers understand how flanges will perform in real-world conditions, improving safety and efficiency. Reliable flanges suppliers are at the forefront of these innovations, ensuring industries can access the high-performance solutions they need.
Flanges are critical in high-pressure and high-temperature systems, especially in demanding industries like oil and gas. They ensure safety, support efficient maintenance, and help keep complex operations running smoothly. Choosing the right materials, following industry standards, and prioritizing regular maintenance are all essential to maximize their performance and durability. With advancements in flange technology continuing to push boundaries, these small but vital components are more reliable and innovative than ever. Whether sourcing flanges for the oil and gas industry or other applications, partnering with trusted flanges suppliers ensures you’re investing in quality and long-term dependability. In challenging environments, it’s often the smallest components that have the biggest impact, making the right choice more important than ever.
FAQ’s
In the oil and gas world, the flanges you’ll see most often are weld neck, slip-on, and blind flanges. These are the go-to options because they handle extreme pressure really well, create tight seals, and make maintenance easier. Reliable flanges suppliers can help you find the best type for your setup.
Flanges designed for high temperatures are made from stainless steel and nickel alloys. These materials are great at handling heat, resisting expansion, and maintaining a proper seal. Most reputable flanges suppliers ensure their products meet strict standards, so they’ll hold up even in the toughest conditions.
Flange leaks can happen for a few reasons—common culprits are loose or over-tightened bolts, worn-out gaskets, or fatigue in the material. Choosing high-quality flanges for the oil and gas industry and working with experienced flanges suppliers can significantly lower the chances of a leak disrupting your operations.
Absolutely. Standards like ASME, ASTM, and ISO ensure that flanges are safe and reliable in high-temperature environments. Trusted flanges suppliers make sure their products follow these strict guidelines so you can be confident they’ll perform as needed.
Regular inspections are key. In most cases, flanges should be checked during maintenance cycles, which are usually every 12 to 18 months. Partnering with a reliable flanges supplier helps you get durable products, which means fewer surprises and smoother inspections over time.