5 Common Types of Flange Used in the Oil and Gas Industry
Flanges play a key role in the oil and gas industry. They connect pipes, valves, pumps, and other equipment to create a secure piping system. They allow easy access for cleaning, inspection, and modifications, ensuring the system stays efficient and reliable. The right flange choice enhances durability and safety, preventing leaks and maintaining smooth operations.
Different types of flanges serve specific purposes, directly influencing performance and maintenance. Selecting the right one can enhance system integrity and minimize downtime. Understanding flange uses and their design, benefits, and uses is important for making smart choices when assembling and maintaining pipelines.
This blog will explore five common flanges for the oil and gas industry, detailing their design, advantages, and typical applications. By the end, readers will clearly understand these flanges and how to choose the right one for their needs.
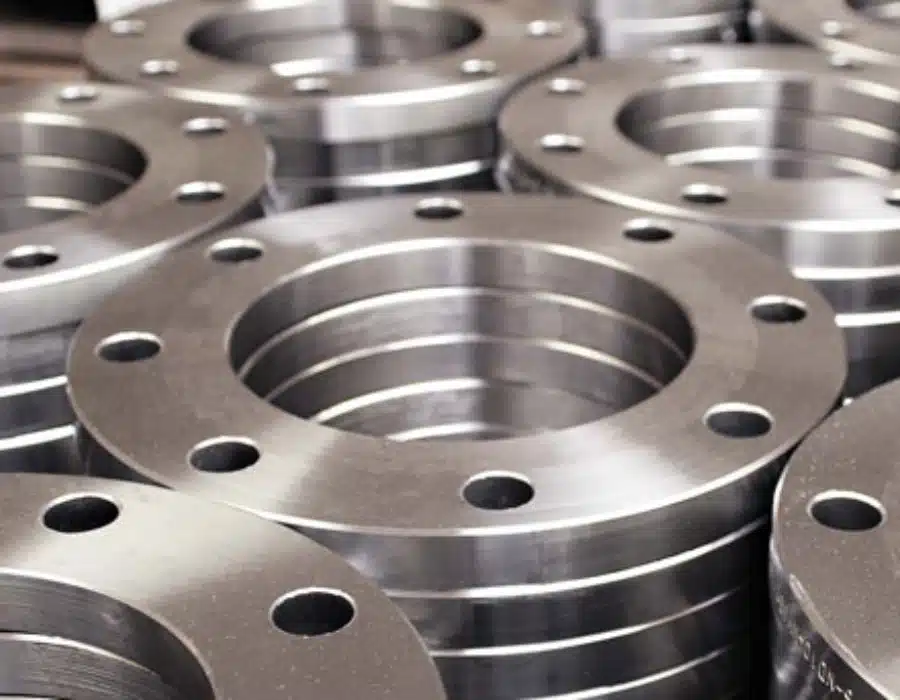
Weld Neck Flange
Weld neck flanges feature a long, tapered neck welded directly to the pipe. This design ensures a smooth transition between the flange and pipe, which helps reduce stress and increases the strength of the connection. Due to their durability, they are commonly used in industrial flanges requiring high performance.
Advantages
- Provides outstanding strength and toughness, making it very reliable for demanding applications.
- Ideal for high-pressure and high-temperature environments, ensuring optimal performance under extreme conditions.
- Minimizes stress concentration, enhancing the longevity and integrity of connections.
- Promotes a smooth and uninterrupted flow of fluids, preventing turbulence and inefficiencies.
Typical Applications
Weld neck flanges are one of the high-pressure systems, such as those found in the flanges of the oil and gas industry, where the integrity of the connection is paramount. Their capacity to withstand high temperatures and pressures makes them vital for key applications.
Slip-On Flange
Design and Fabrication
Slip-on flanges are made to slide over the pipe and then be welded into place. They are much easier to align and install than weld neck flanges, making them a popular choice for flange uses that need quick installation.
Advantages
- Simple and quicker to install, saving both time and effort.
- Lower upfront cost compared to weld neck flanges, making it budget-friendly.
- Works well in low-pressure systems and non-critical applications.
- It requires less precise pipe cutting, simplifies installation, and reduces labour.
Limitations
- Less strong and durable compared to weld neck flanges.
- It is not suitable for systems with high pressure or high temperatures.
- Needs double welding for a secure and leak-proof connection, increasing labor effort.
- Limited lifespan in demanding or harsh environments.
Common Uses
Slip-on flanges are frequently utilized in low-pressure applications where ease of installation and cost efficiency are more important than the strength of the connection. These industrial flanges are commonly found in water pipelines, cooling systems, and low-pressure steam lines, making them a versatile choice for various non-critical systems.
Socket Weld Flange
Socket weld flanges feature a socket that the pipe fits into, followed by welding around the joint. This design provides a smooth bore and better flow characteristics, making them highly effective in high-pressure applications.
Advantages
- Offers a smooth bore, improving fluid flow and reducing resistance.
- Ideal for small-diameter pipes handling high-pressure applications.
- Provides a strong and dependable connection, ensuring system reliability.
- Minimizes the risk of leaks due to its internal welding process.
- Durable enough for long-term use in vital systems.
- Maintains consistent performance in challenging environments.
Disadvantages
- It is not practical for larger pipe sizes due to design limitations.
- Requires accurate and skilled welding to create a secure and leak-free connection.
- Installation can take more time and effort, increasing labour costs.
Where It’s Used
Socket weld flanges are typically used in high-pressure systems with small pipe diameters, such as those found in the oil and gas industry flanges. They are ideal for piping systems that handle hazardous fluids, ensuring a strong and leak-free connection.
Blind Flange
Blind flanges are used to close off pipe ends or openings in pressure vessels. They do not have a bore and are essentially solid disks, making them perfect for blocking off pipelines.
Advantages
- Provides a strong and secure seal to close off pipelines or openings.
- Makes it easy to access the system for inspections, cleaning, or maintenance.
- Can handle high-pressure conditions effectively and prevent leaks.
- Useful for pressure testing to ensure the system’s strength and reliability.
- Durable and versatile, it is suitable for a variety of industrial applications.
- Easy to remove or replace when needed, offering flexibility in operations.
Practical Applications
Blind flanges are widely used in systems designed for future expansion or maintenance, particularly in oil and gas industry flanges. They are essential for isolating pipeline sections, allowing shutdowns without interrupting the entire system’s operation.
Threaded Flange
Threaded flanges are designed with a threaded bore, allowing them to be screwed directly onto pipes without the need for welding. This makes them an excellent choice for systems where welding is dangerous or impractical, such as in explosive or flammable environments.
Pros
- Quick to install and remove, making it easier and faster.
- Does not require welding, reducing installation complexity.
- Works well in high-pressure systems, ensuring reliable performance.
- Safe to use in hazardous areas where welding is restricted or risky.
- Cost-effective for temporary or maintenance applications.
Cons
- It is unsuitable for high-temperature systems, as threads may fail under extreme heat.
- Threads can wear out over time, reducing connection reliability.
- Limited to smaller pipe sizes, as larger diameters require more robust solutions.
Typical Usage
Threaded flanges are often used in low-pressure, non-critical applications where welding is impractical or impossible. They are the best for industrial types of flanges, especially for small-diameter pipe connections in plumbing and fire protection systems.
Comparative Summary of the 5 Flanges
Key Differences at a Glance
Flange Type | Cost | Pressure/Temperature Handling | Ease of Installation |
Weld Neck | High | High | Complex |
Slip-On | Low | Low | Easy |
Socket Weld | Moderate | High | Moderate |
Blind | Moderate | High | Easy |
Threaded | Low | Moderate | Easy |
Selecting the Right Flange for Your Application
When choosing among the industrial types of flanges, consider the pressure, temperature, and environmental conditions of your application. High-pressure and high-temperature systems typically require durable options, such as weld neck or socket weld flanges, specially made to resist extreme conditions and provide safe, efficient performance.
Service Frequency
If your system requires frequent maintenance or disassembly, use easier flanges to install and remove, such as slip-on or threaded flanges. This reduces downtime and labour costs, making your maintenance processes more efficient and cost-effective. Easy-to-install flanges can significantly improve operational efficiency.
Regulatory and Safety Standards
Ensure that the flanges for the oil and gas industry meet industry standards and regulations. Compliance with safety protocols guarantees system reliability and longevity, prevents accidents, and ensures smooth operations. Following these standards is important for keeping your piping systems safe and in good condition.
Cost vs. Performance
Balancing the flange’s initial cost with its performance and longevity is essential. A higher-quality flange can save you money over time by lowering maintenance costs, reducing downtime, and preventing safety risks. High-quality flanges offer better durability and reliability, providing long-term benefits for your operations.
Conclusion
Understanding the various industrial types of flanges and their specific uses is essential for optimizing piping system performance and safety in the oil and gas industry. The right flange choice makes the system more durable, guarantees a secure connection, and reduces the risk of leaks or failures. Factors such as pressure rating, material compatibility, and environmental conditions are key in choosing the appropriate flange. Making well-informed decisions helps improve system performance, save on maintenance costs, and lengthen the lifespan of your infrastructure, ensuring smooth running in demanding industrial conditions.
FAQs
What are the different types of flanges?
There are various industrial types of flanges, including weld neck, slip-on, socket weld, blind, and threaded flanges. Each serves a specific function: a weld neck offers high strength, slip-on is easy to install, socket weld is ideal for small pipes, blind sealing off pipelines, and threaded is used for low-pressure applications.
What type of flange is ASME?
ASME flanges meet the standards set by the American Society of Mechanical Engineers (ASME). They ensure compatibility, reliability, and safety in industrial applications. With strict design, material, pressure, and size guidelines, these flanges are frequently used in piping systems of oil and gas, chemical, and power industries.
What are FF and RF flanges?
FF (Flat Face) flanges have a smooth, flat sealing surface and are commonly used in low-pressure applications. RF (Raised Face) flanges feature a raised sealing surface, which concentrates pressure on a smaller gasket area, improving sealing effectiveness. RF flanges are preferred in high-pressure, high-temperature environments for better leak prevention and durability.