Ten Essential Types of Pipes Used in the Oil and Gas Industry
The oil and gas industry uses specialized pipes to transport fluids like crude and natural gas from extraction sites to refineries and end users. These pipes must withstand extreme conditions, including high pressure, harsh temperatures, and corrosive substances, making their selection critical to the safety and efficiency of operations.
Understanding the various types of pipes and their specific applications is key to choosing the right materials for different projects. This blog offers a clear and comprehensive overview of the most commonly used pipes in the oil and gas sector, providing industry professionals with the knowledge they need to make well-informed decisions.
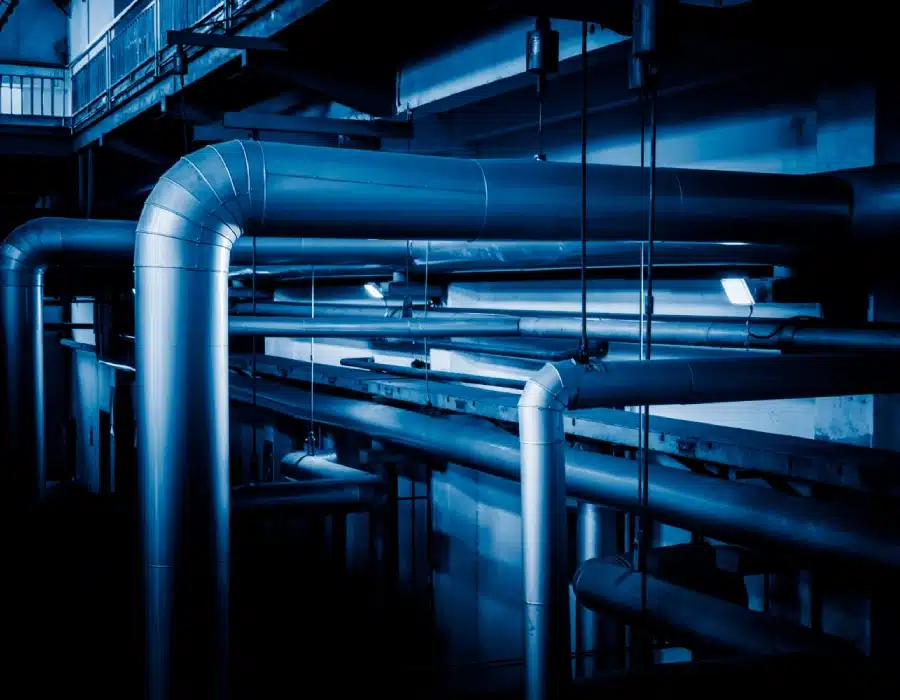
Carbon Steel Pipes
Carbon steel pipes, made from iron and carbon, are strong and durable. Commonly used in the oil and gas industry, these pipes can withstand high pressure and harsh conditions, making them perfect for transporting oil and gas. Their low cost and dependability make them a popular choice for industrial use.
Key Advantages
- High strength and long-lasting durability
- Affordable and cost-effective
- Can handle high-pressure environments
Common Applications
Carbon steel pipes are used in refineries, pipelines, and oil and gas plants to transport fluids safely over long distances. Their strength under tough conditions makes them reliable for these tasks. They are also widely used in structural and mechanical applications within the industry.
Stainless Steel Pipes
Stainless steel pipes, composed of iron, chromium, and other elements, offer excellent resistance to rust and corrosion. Available in grades 304, 316, and 410, they serve different purposes. Grade 304 is versatile, grade 316 resists corrosion in harsh environments, and grade 410 is known for its high strength.
Advantages
- Excellent resistance to rust and corrosion
- Strong and durable
- Can handle high temperatures effectively
Industry Uses
Stainless steel pipes are often used in water systems, the oil industry, and chemical plants. Their strength and cleanliness make them ideal for food processing, pharmaceutical industries, and construction projects.
Alloy Steel Pipes
Alloy steel pipes combine steel with elements like chromium, molybdenum, and nickel. They enhance their performance in extreme conditions. Alloy steel pipes come in various grades, each made for specific industrial needs, like better heat resistance or increased toughness for tough conditions.
Why Does Alloy matter?
Alloy steel pipes provide exceptional performance in challenging environments. They can handle high pressure and extreme temperatures, making them ideal for demanding industrial applications. Their enhanced properties make them more reliable and long-lasting than standard steel pipes.
Common Uses
Alloy steel pipes find use in power plants, oil and gas refineries, and chemical facilities. They are also found in systems like boilers and heat exchangers, where strength and heat resistance are important.
Duplex Stainless Steel Pipes
Duplex stainless steel pipes feature a mixed microstructure of austenite and ferrite, providing greater strength and corrosion resistance than traditional stainless steel pipes. They perform well in harsh environments, including saltwater and acidic conditions.
Advantages
- High strength for demanding applications
- Great resistance to corrosion, especially in tough environments.
- Good weldability, making installation easier and more efficient
Applications
Duplex stainless steel pipes are used in chemical plants, oil and gas exploration, marine environments, and offshore platforms. They are also perfect for desalination plants, heat exchangers, and storage tanks.
Nickel Alloy Pipes (e.g., Inconel, Monel)
Nickel alloy pipes, made from nickel combined with chromium, molybdenum, or copper, offer superior heat and corrosion resistance. Inconel is known for heat resistance, while Monel provides excellent corrosion resistance, especially in marine environments.
Standout Qualities
- High resistance to heat and corrosion, even in harsh environments
- Excellent mechanical properties, including strength and durability
- Long-lasting performance, reducing maintenance needs
Typical Uses
Nickel alloy pipes are commonly used in high-temperature applications like gas turbines, heat exchangers, and chemical processing equipment. They are also used in the aerospace industry, power plants, and marine systems, where their ability to withstand extreme temperatures and corrosive substances is critical.
Seamless Pipes
Seamless pipes are made by pushing a solid piece of metal through a mould to form a hollow tube without welding. This process ensures even strength, better reliability, and durability. The lack of weld seams reduces weak spots, improving performance under pressure and tough conditions.
Advantages
- High strength and durability for demanding applications
- No weld seams, minimizing the risk of leaks or failures
- Suitable for high-pressure and high-temperature environments
Industry Applications
Seamless pipes are used in industries like oil and gas exploration, power plants, and chemicals. They are also used in boilers, heat exchangers, and hydraulic systems because they can withstand tough conditions.
Welded Pipes (ERW, LSAW, SSAW)
ERW (Electric Resistance Welded)
ERW pipes are made by welding steel strips, making them cost-effective and ideal for low to medium-pressure applications, such as urban oil and gas transport.
LSAW (Longitudinal Submerged Arc Welding)
LSAW pipes are made by welding the edges of a steel plate along its length. They are designed for high-pressure applications, long-distance pipelines, and demanding environments, including offshore and underground systems.
SSAW (Spiral Submerged Arc Welding)
SSAW pipes are produced by spirally welding a steel coil. They are suitable for large-diameter pipelines, low-pressure systems, and projects requiring flexibility in pipe lengths.
Key Advantages
- Cost-effective and economical for large-scale projects
- Suitable for various pressure levels, from low to high
- Available in large diameters for versatile applications
Where They Fit
Welded pipes transport oil and gas, supply water, and build projects like bridges and construction. Their versatility and affordability make them essential for infrastructure and industrial needs.
Plastic Pipes (HDPE, GRE/GRP)
High-Density Polyethylene (HDPE) Pipes
HDPE pipes are made from high-density polyethene, offering excellent resistance to corrosion, chemicals, and UV radiation. Their lightweight and flexible nature makes them ideal for cross-country pipelines, irrigation systems, and water supply networks. They are also durable and have long service life even in harsh environments.
Glass Reinforced Epoxy/Polyester (GRE/GRP) Pipes
GRE/GRP pipes are made from glass fibres reinforced with epoxy or polyester resin. These pipes are strong, lightweight, and highly resistant to corrosion, making them suitable for carrying water, chemicals, and other fluids in industries like oil and gas and desalination plants.
Advantages and Limitations
- Resistant to corrosion, chemicals, and environmental wear
- Lightweight and easy to transport and install
- Limited to low-pressure applications and may not be suitable for high-temperature fluids
Plastic pipes are commonly used in industries as cost-effective, low-maintenance solutions, especially for transporting water and chemicals. Their flexibility and ease of handling make them a popular choice for various infrastructure projects.
Clad/Lined Pipes
Clad or lined pipes have a layer of corrosion-resistant material, such as stainless steel, bonded to a carbon steel pipe. This combination delivers the strength and toughness of carbon steel, along with the necessary corrosion resistance for harsh environments.
Why Use Clad or Lined Pipes?
Clad or lined pipes are ideal for applications where corrosion resistance is crucial, such as when transporting aggressive or corrosive fluids. The cladding or lining provides added protection without compromising the pipe’s strength or flexibility.
Examples of Usage
These pipes are often used in offshore oil and gas production, chemical plants, and power generation. They are also found in water treatment plants and desalination facilities, where their corrosion protection ensures long-lasting performance and reliability.
Selection Criteria for Oil and Gas Piping
Pressure and Temperature Requirements
Pipes must be able to handle the application’s specific pressure and temperature conditions. For example, pipelines in deep-sea drilling need to withstand higher pressures and colder temperatures than those in surface-level operations.
Corrosive Fluids and Environments
Selecting pipes with the right level of corrosion resistance is essential when transporting aggressive fluids, such as oil, gas, or chemicals. Pipes that can withstand harsh environments prevent leaks and damage, ensuring safe operations.
Regulatory and Safety Standards
Pipes must meet industry standards and regulations, such as those set by organizations like ASME and API, to ensure safety, reliability, and environmental protection. Compliance with these standards also reduces the risk of costly accidents or failures.
Cost vs. Performance Balance
Finding the right balance between cost and performance is key. While high-quality, durable pipes may cost more upfront, their long-term reliability and fewer maintenance needs can make them more economical in the long run. This balance helps ensure both efficiency and cost-effectiveness.
Conclusion
Understanding the different
FAQs
What types of pipes are used in the oil and gas industry?
Various types of pipes are used in the oil and gas industry. They include carbon steel, stainless steel, alloy steel, duplex stainless steel, nickel alloy, seamless, welded, plastic (HDPE, GRE/GRP), and clad/lined materials. These pipes are chosen based on pressure, temperature, and corrosion resistance.
What are the 3 types of pipelines that carry oil?
The three types of pipelines that carry oil are gathering pipelines, which collect oil from production sites; transmission pipelines, which transport oil over long distances; and distribution pipelines, which deliver oil to refineries or end users. Each type serves a distinct function in the transportation process. Oil and gas pipe suppliers provide the necessary materials for these pipelines to ensure efficient and safe oil transport.
What are the different types of gas pipes?
Gas pipelines use pipes made of carbon steel, stainless steel, alloy steel, and plastic materials like HDPE and GRE/GRP. The choice of material depends on factors like the type of gas, the environment, pressure requirements, and the need for corrosion resistance or ease of installation. These materials are some of the common types of pipe used in the gas industry to ensure safe and efficient transport.