Types of Flanges - Advantages and Disadvantages
Flanges are important parts of piping and engineering systems. They provide a dependable way to connect pipes, valves, pumps, and other equipment, helping to keep these systems strong and working efficiently. They are crucial for assembling and disassembling piping systems, making maintenance, inspection, and modifications easier. Flanges offer secure, leak-proof connections, vital for the safe and smooth operation of industrial processes while also helping to align pipes and ensure proper fluid flow. This article will give an overview of the different types of flanges, how they are made, their advantages and disadvantages, and where they are commonly used. It will also explore the materials and standards related to flanges, helping you make informed decisions when choosing them for your projects.
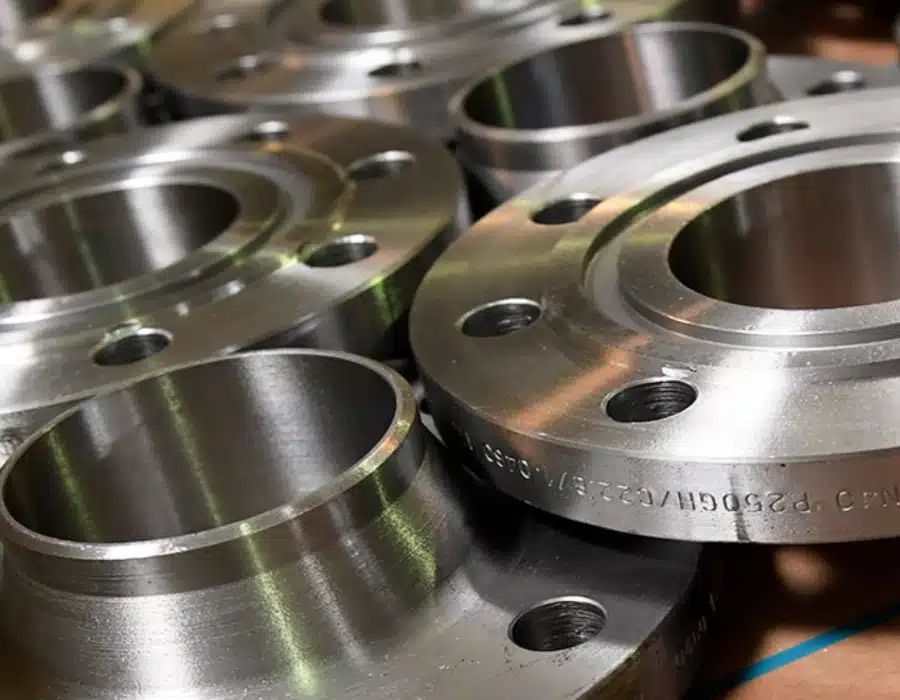
What Are Flanges?
Flanges are tools that securely connect pipes and other equipment, preventing leaks in a piping system. These disc-shaped components feature bolt holes, allowing them to be easily assembled, disassembled, and maintained.
Flanges can be welded or screwed onto pipes, providing a strong and reliable connection that is essential for the integrity and efficiency of the system. Their design and versatility make them crucial for smooth operations, offering a simple yet effective solution for connecting various parts of a piping system.
Role in Piping Systems
In piping systems, flanges serve several critical functions:
- Connection: They join pipes and components, ensuring a continuous flow path.
- Access: Flanges allow easy access to the system for cleaning, inspection, and modifications.
- Strength: They provide mechanical support, enhancing the system’s structural integrity.
- Sealing: Using gaskets, flanges create a tight seal, preventing leaks.
Common Types of Flanges
Common flanges are used in piping systems, each with advantages and disadvantages. Here are some of the most common types of Flanges:
Weld Neck Flange
How It’s Made:
Weld neck flanges are created by shaping solid metal into the needed form. They are then welded to the pipe, creating a strong and dependable connection.
Advantages:
- High strength and durability
- Suitable for high-pressure and high-temperature applications
- Ensures a smooth flow from the flange to the pipe, lowering stress in the connection.
Disadvantages:
- More expensive due to the forging process
- Requires skilled welding for proper installation
Typical Applications:
Weld neck flanges are ideal for high-pressure and high-temperature situations in industries like oil and gas, power plants, and chemical processing.
Slip-On Flange
How It’s Made:
Slip-on flanges are made by cutting a hole in the centre of a flat piece of metal and then welding it to the pipe. The pipe fits into the flange and is welded inside and outside.
Advantages:
- Easier and faster to install compared to weld neck flanges
- Less expensive due to simpler manufacturing process
- Suitable for low-pressure applications
Disadvantages:
- Lower strength and durability compared to weld neck flanges
- Not suitable for high-pressure or high-temperature applications
Typical Applications:
Slip-on flanges are frequently used in low-pressure applications, such as water and gas systems and general industrial piping.
Socket Weld Flange
How It’s Made:
Socket weld flanges are made by machining a socket into the flange, where the pipe is inserted and welded. This creates a strong and reliable connection.
Advantages:
- Provides a strong and leak-proof connection
- Suitable for small-diameter, high-pressure applications
- Easier to align compared to butt-welded joints
Disadvantages:
- Not suitable for large-diameter pipes
- Requires skilled welding for proper installation
Typical Applications:
Socket weld flanges are commonly found in small, high-pressure piping systems, like hydraulic and steam lines.
Lap Joint Flange
How It’s Made:
Lap joint flanges are made by machining a flat piece of metal into the desired shape. The flange is then used with a stub end welded to the pipe.
Advantages:
- Allows for easy alignment and adjustment
- Suitable for applications requiring frequent disassembly
- Less expensive than weld neck flanges
Disadvantages:
- Lower strength and durability compared to weld neck flanges
- Not suitable for high-pressure or high-temperature applications
Typical Applications:
Lap joint flanges are often utilized in systems that need regular disassemblies, such as for maintenance, repairs, and inspections because they are easy to put together and take apart.
Threaded Flange (Screwed Flange)
How It’s Made:
Threaded flanges are made by machining threads into the flange, allowing it to be screwed onto the pipe. This creates a strong and reliable connection without the need for welding.
Advantages:
- Easy to install and remove
- Suitable for low-pressure applications
- No welding is required, reducing installation time and cost.
Disadvantages:
- Not suitable for high-pressure or high-temperature applications
- Threads can be prone to corrosion and wear.
Typical Applications:
Threaded flanges are typically used in systems with low pressure, like water and gas distribution and industrial piping.
Blind Flange
How It’s Made:
Blind flanges are made by machining a solid piece of metal into the desired shape. They are used to close off the end of a piping system.
Advantages:
- Provides a secure and leak-proof seal
- Suitable for high-pressure and high-temperature applications
- It can be used for pressure testing of piping systems.
Disadvantages:
- More expensive due to the solid construction
- Requires skilled installation to ensure a proper seal
Typical Applications:
Blind flanges seal off pipe ends in applications like pressure testing and maintenance.
Reducing Flange
How It’s Made:
Reducing flanges are made by machining a flat piece of metal into the desired shape, with a smaller diameter opening in the centre. This allows pipes of different sizes to be joined together.
Advantages:
- Makes it possible to connect pipes of different sizes.
- Suitable for low-pressure applications
- Less expensive than using reducers and flanges separately
Disadvantages:
- Not suitable for high-pressure or high-temperature applications
- Requires skilled installation to ensure a proper seal
Typical Applications:
Reducing flanges are commonly used in systems where pipes of different diameters need to be connected, such as in water and gas distribution systems.
Materials and Standards
Common Materials
Flanges are made from different materials to match various working conditions. Some common materials include:
- Carbon Steel – This material is used for general applications due to its strength and cost-effectiveness.
- Stainless Steel is corrosion-resistant, making it perfect for the chemical and food processing industries.
- Alloy Steel – Used in high-temperature and high-pressure environments.
- Cast Iron – Common in older plumbing and low-pressure applications.
- PVC & Plastic – Lightweight and corrosion-resistant, mainly used for water and chemical pipelines.
Relevant Standards
Flange suppliers must adhere to international standards to guarantee compatibility, safety, and performance. Key standards to consider include:
- ASME B16.5 – Encompasses pipe flanges and flanged fittings.
- ASTM Standards – Define the material composition and mechanical properties.
- ISO 7005 – International standard for steel flanges.
- EN 1092-1 – European standard for flanges.
Advantages and Disadvantages Overview
Comparative Table
Types of Flange | Advantages | Disadvantages | Typical Applications |
Weld Neck Flange | High strength, suitable for high-pressure | Expensive, requires skilled welding | Oil and gas, power plants, chemical processing |
Slip-On Flange | Easy to install, cost-effective | Lower strength, not for high-pressure | Water and gas distribution, industrial piping |
Socket Weld Flange | Strong connection, suitable for small-diameter | Not for large diameters, requires skilled welding | Hydraulic and steam lines |
Lap Joint Flange | Easy alignment, cost-effective | Lower strength, not for high-pressure | Maintenance and inspection applications |
Threaded Flange | Easy to install, no welding required | Not for high-pressure threads prone to wear | Water and gas distribution, industrial piping |
Blind Flange | Secure seal, suitable for high-pressure | Expensive, requires skilled installation | Pressure testing, maintenance applications |
Reducing Flange | Connects different diameters, cost-effective | Not for high-pressure, requires skilled installation | Water and gas distribution |
Summary of Key Points
- Flanges are important in piping systems, making them easy to assemble, take apart, and maintain.
- Various flanges are used based on pressure, temperature, and connection needs.
- Weld neck flanges are best for high-pressure applications, while slip-on flanges are cost-effective for low-pressure systems.
- Selecting the right flanges suppliers ensures that materials from carbon steel to stainless steel follow international safety standards and are compatible with different products.
- Selecting the right flange type depends on application-specific requirements such as pressure, temperature, and ease of maintenance.
Conclusion
Choosing the right flanges is critical for ensuring the efficiency, safety, and longevity of piping systems. Each flange type has unique characteristics that make it suitable for specific applications. Knowing each flange’s advantages and disadvantages helps engineers and decision-makers choose the most suitable option.
When sourcing flanges, working with reliable suppliers who provide high-quality, industry-standard products ensures optimal performance and safety.
FAQs
Which flange is best for high-pressure, high-temperature applications?
Weld neck flanges are ideal for high-pressure, high-temperature applications due to their tapered hub, which evenly distributes stress and provides exceptional strength. Their strong design reduces the chance of leaks, making them a dependable choice for tough industrial systems.
Can I use a threaded flange for chemical processes?
Threaded flanges, one of the common types of flanges, are generally unsuitable for chemical processes because their threads can create leakage points and may not withstand corrosion from aggressive chemicals. Flanges made from corrosion-resistant materials and with welded connections are more suitable for such environments, ensuring safety and durability.
Do all flanges require welding?
No, not all flanges require welding. Threaded flanges, offered by many flanges suppliers, can be screwed onto pipes, making them ideal for explosive environments. Similarly, lap joint flanges, also available from flanges suppliers, rely on a loose connection with a stub end, eliminating the need for welding and offering flexibility in assembly and disassembly.